Optimizing Warehouse Labor Management in a Changing Landscape
As labor costs rise and workforce availability declines, companies are facing pressure to rethink how they approach warehouse labor. Automation and AI are top priorities, but these technologies alone won’t...
Strategies for a Future-Ready Workforce
On November 18, 2024
As labor costs rise and workforce availability declines, companies are facing pressure to rethink how they approach warehouse labor. Automation and AI are top priorities, but these technologies alone won’t eliminate the need for human workers. Instead, successful strategies for labor management in warehouses are about maximizing efficiency within current labor constraints, standardizing processes, and leveraging data-driven decisions across distributed facilities.
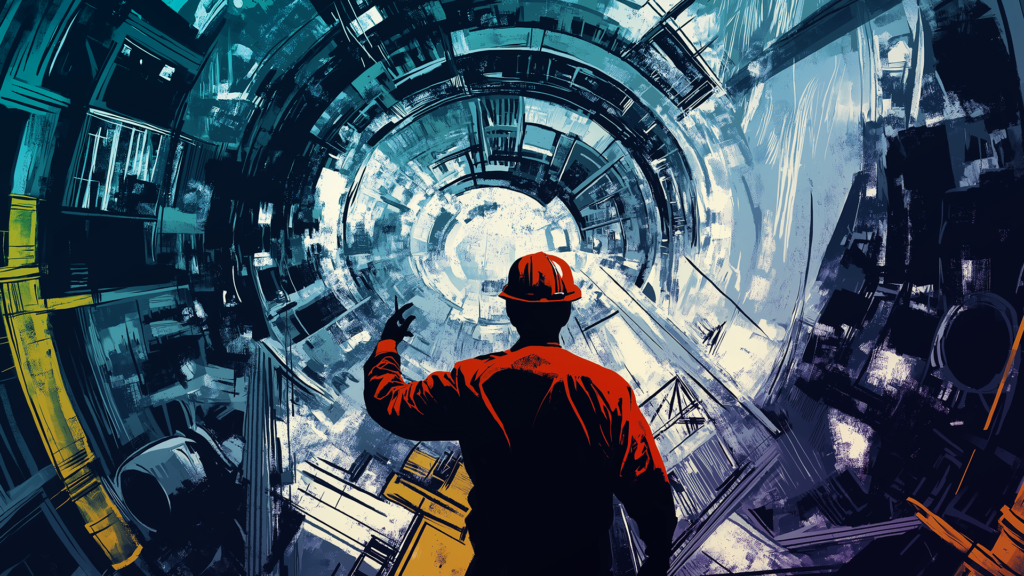
Understanding the Shifting Labor Landscape
The modern labor market presents two significant challenges: increasing labor costs and a shrinking labor pool. These shifts have driven organizations to explore automation, not as a luxury, but as a necessity. Companies are not asking if they should automate but rather when and where to implement these technologies. However, a successful automation strategy requires a solid foundation in labor management.
Before diving into automation, companies must assess their existing workforce capabilities. A clear understanding of current labor usage allows for a more accurate return on investment (ROI) when automation or other technologies are introduced. By optimizing labor utilization—potentially even achieving small efficiency gains of just 3% to 5%—companies can realize substantial savings when scaled across a network of warehouses. This approach underscores the importance of labor management strategies that emphasize consistency, measurement, and a network-wide view of operations.
Never miss a story. Stay updated about Rebus news as it happens.
Standardization Across Warehouse Networks
A common issue across large warehouse networks is data fragmentation. Many facilities operate with distinct systems or tools, often due to regional differences, acquisitions, or specific customer needs. This diversity complicates data analysis and hampers efficiency. By focusing on standardizing processes, companies can break down data silos and streamline reporting.
For example, standardized labor practices—such as method-based standards—can help establish consistent operational benchmarks across facilities. Method-based standards involve creating predefined approaches to common tasks, such as unloading a pallet or picking an order. This consistency ensures that all facilities operate with the same baseline, allowing for more reliable performance metrics and easier cross-facility comparisons.
One crucial benefit of standardization is its impact on scalability. When even minor efficiencies are achieved at one site, they can be applied across the network, creating a cumulative effect that leads to significant cost savings. Consistency in labor practices also promotes easier training and resource sharing. This strategy not only reduces errors but also fosters a shared culture of continuous improvement across the organization.
The Role of Data in Effective Labor Management
Data is a cornerstone of effective labor management, especially when it comes to tracking productivity, identifying inefficiencies, and making informed decisions. Companies need visibility into key performance indicators (KPIs) such as productive versus non-productive hours, overtime usage, and training time. Without real-time data, managers are often forced to rely on retrospective reports, which can lead to missed opportunities for immediate adjustments.
A centralized data platform enables real-time insights across the entire network, giving managers the tools to make on-the-fly adjustments and allocate resources efficiently. With standardized data and shared terminology across sites, facilities can engage in more meaningful comparisons, driving accountability and fostering a competitive spirit that motivates teams to improve their performance.
Leveraging Best Practices Through Network Visibility
Standardizing data not only provides operational benefits but also opens opportunities for continuous improvement. When all facilities speak the same “data language,” it’s easier to identify high-performing sites and pinpoint best practices. Companies can then share these successes across the network, enabling a “learn and replicate” model that fosters consistent improvements without reinventing the wheel at each location.
For example, a site that demonstrates exceptional efficiency in one process—such as order picking—can serve as a benchmark. Other facilities can adopt these practices, improving overall network efficiency. Additionally, having a single source of truth for data reduces time-consuming report generation, allowing regional and corporate managers to focus on strategic initiatives rather than operational troubleshooting.
Sustaining Long-Term Success in Labor Management Programs
Many companies invest heavily in labor management programs upfront, only to see these efforts falter over time. This breakdown often occurs because of shifting priorities, staff turnover, or changes in systems. To prevent this, organizations must implement a sustainment strategy that includes regular updates to labor standards and processes.
A key aspect of sustainment is change control. As companies adjust their systems and processes—whether through feature updates, process changes, or new equipment—there must be a mechanism to assess the impact on labor standards. For example, if a scanning process changes, the time allocation in labor standards should be updated accordingly. This continuous alignment ensures that labor standards remain accurate and useful across all sites, supporting consistent performance and avoiding unnecessary rework.
Another essential component of sustainment is utilizing data to monitor program health. By tracking labor metrics across the network, companies can identify anomalies early on, enabling preemptive actions to address potential issues. Regular data reviews and updates keep programs relevant, avoiding the costly cycle of program reinvention.
Enhancing Employee Engagement Through Data-Driven Insights
Labor management programs should not only focus on productivity and cost efficiency but also consider employee engagement. With a strong labor program backed by data, managers can have more productive conversations with team members, helping them to understand their roles, develop skills, and grow within the company.
For example, by providing real-time data on performance metrics, employees receive immediate feedback on their efforts. Managers can use this data to recognize top performers and identify areas for improvement, creating an environment where everyone is working toward a shared goal. This level of transparency fosters a sense of ownership and pride in their work, which in turn can improve retention and job satisfaction.
How to optimize warehouse labor management:
- Understand the shifting labor landscape
- Standardize across warehouse networks
- Get visibility into KPIs
- Leverage best practices through network visibililty
- Implement a sustainment strategy that includes regular updates to standards and processes
- Enhance employee engagement through data-driven insights
Conclusion
As the warehouse labor market continues to evolve, companies must adopt a proactive approach to labor management that leverages technology, standardization, and data. Automation and AI will play crucial roles, but human workers remain essential. A standardized, data-driven approach to labor management allows companies to optimize existing resources, improve network-wide efficiencies, and foster a competitive, engaged workforce.
In this era of transformation, the companies that will succeed are those that treat labor management as a strategic asset, using data to drive continuous improvement, sustain long-term program benefits, and create a unified, competitive culture across their entire network. As challenges continue to arise, having a robust labor management strategy is more critical than ever, helping businesses not only survive but thrive in a competitive landscape.