Smarter Warehouse Management Starts with Visibility
Most warehouses spend a lot of time and energy on labor planning. Building schedules, assigning roles, and hoping things go according to plan. But plans don’t pick orders. People do....
On July 8, 2025
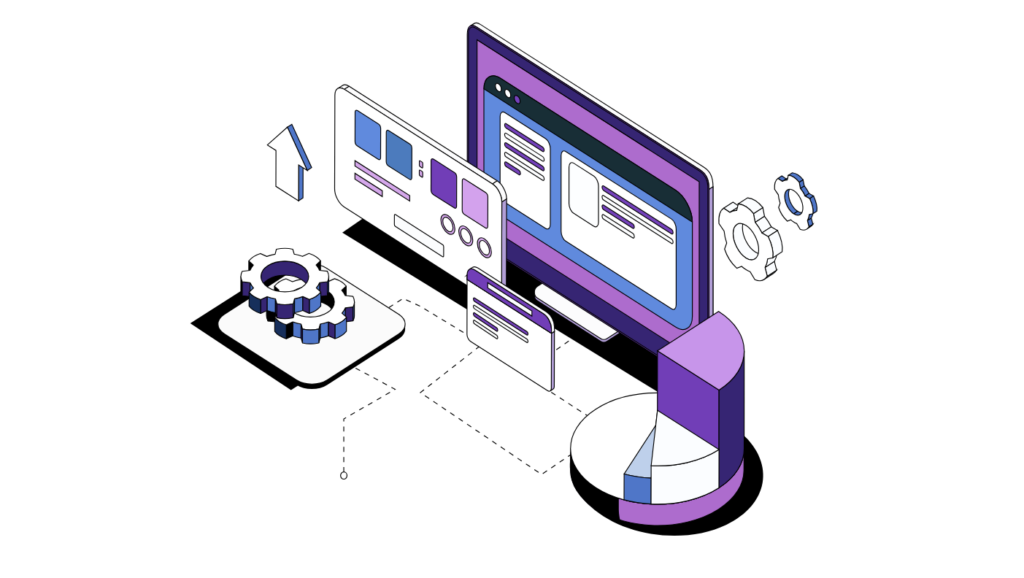
Most warehouses spend a lot of time and energy on labor planning. Building schedules, assigning roles, and hoping things go according to plan. But plans don’t pick orders. People do. And when the volume shifts or a task falls behind, it’s not the plan that saves the day, it’s warehouse visibility.
The truth is, you can’t manage what you can’t see. And in a busy warehouse, that lack of visibility can cost you. Time. Efficiency. Service levels. Even your workforce’s engagement. That’s why smarter warehouse management doesn’t start with staffing, it starts with seeing what’s happening right now.
With Rebus I&PA (Inventory & Process Analytics), you get a live window into inventory and activity across your facility. And that means better decisions, faster reactions, and a more agile operation, shift after shift.
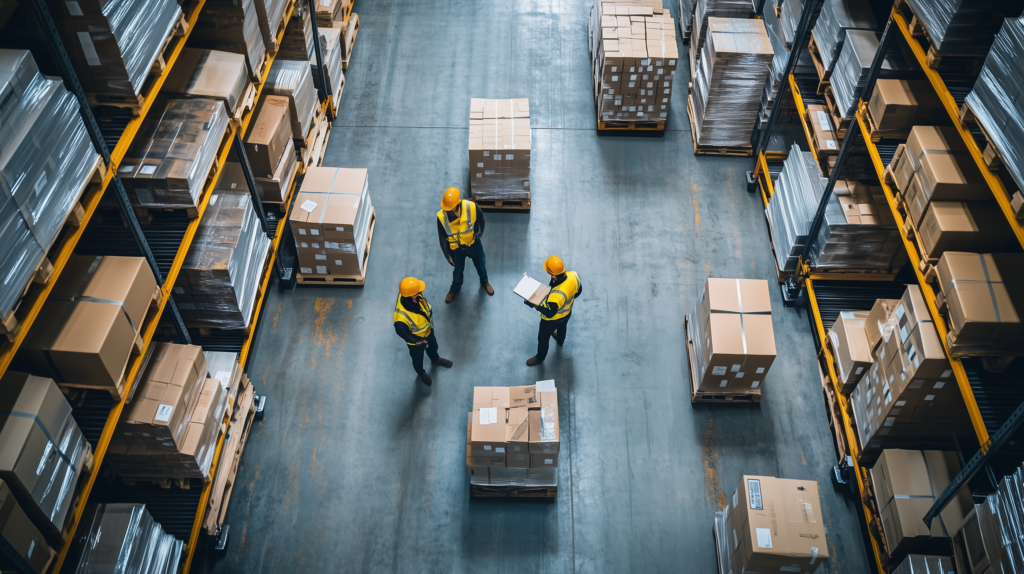
Stop Guessing, Start Seeing
Ask most warehouse supervisors how their teams are doing mid-shift, and they’ll give you an educated guess. Maybe they did a walk-through. Maybe they’ve got someone in their ear saying picking is behind. Maybe they’re staring at a spreadsheet from two hours ago.
That’s not enough.
Rebus I&PA flips the script. Instead of relying on gut feel, warehouse leaders get real-time warehouse visibility into their performance insights: what’s being picked, where delays are forming, and which zones need attention right now. It’s all in one place. No bouncing between systems. No waiting for a report to run. Just immediate, actionable data.
Need to see which workers are overperforming? It’s there. Want to know who’s behind or idle? You’ve got it. Trying to understand why dock-to-stock is slipping this hour? Click into the view and drill down.
This kind of visibility is a game changer. It takes the blindfold off.
Warehouse Visibility Isn’t Static, Your Tools Shouldn’t Be Either
Warehouse work is fluid. One minute, your receiving team is flying through pallets. The next, your outbound side is slammed and you’re short on pickers. The ability to adjust in real time is where you win.
With real-time warehouse visibility from I&PA, you can reallocate tasks dynamically based on real data. See that Jake is outperforming in receiving and you’re falling behind in picking? Move him over. Notice that a certain zone has cleared its workload early? Shift those team members to support another area.
You can even filter by active shipments and see exactly where the work is piling up. Not just a list of picks—a visual map showing where the effort needs to go. That’s how supervisors stop reacting and start orchestrating.
And this isn’t guesswork. You’re not just hoping someone can handle the reassignment. With historical performance data, you can identify which workers are strong pickers, which ones thrive on the dock, and who’s best suited for high-priority tasks.
That’s data-informed decision-making, and it leads to better throughput, more consistent service, and a team that knows their strengths are being put to good use.
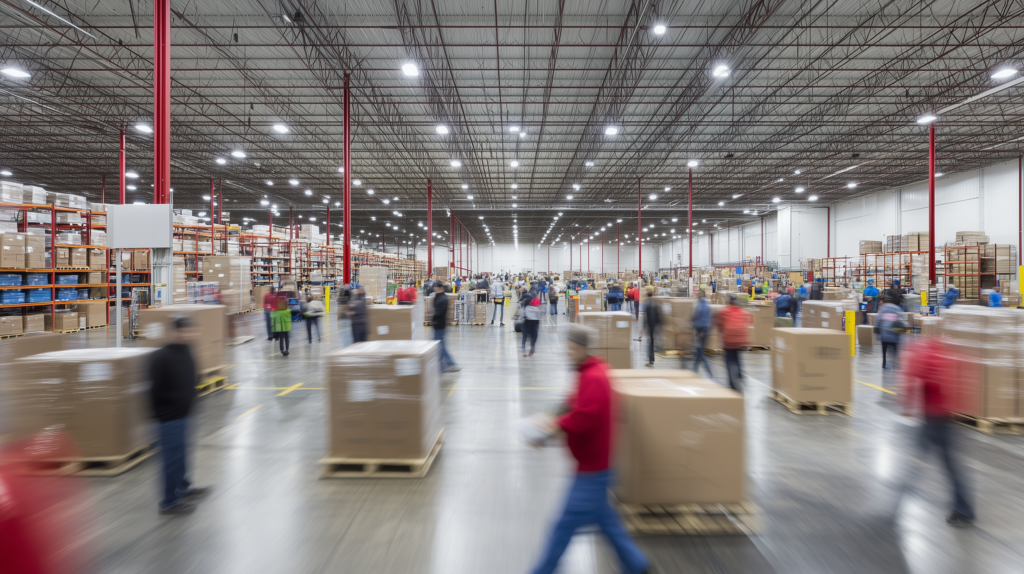
Combining People, Performance, and Context
Here’s the magic: Rebus doesn’t just give you warehouse visibility. It gives you context.
You’re not just looking at people. You’re looking at people doing the work, where the work is, and what needs to happen next. All in one unified system.
You can filter by task type, shift, performance level, even open orders tied to a shipment. You can identify your top pickers and see what they’re doing in the moment. And if they’re stuck on a low-priority task? You can reassign them to where it matters most.
That kind of control isn’t just helpful—it’s empowering. It gives supervisors the confidence to make fast calls without second-guessing. It gives ops leaders a clearer picture of their day. And it gives your warehouse the agility to meet demand as it unfolds, not hours later.
No More “Fire Drills”
We’ve all been there: the daily scramble to hit cutoff windows, reassign teams, and play traffic cop on the fly. It’s stressful. It’s reactive. And it’s completely avoidable when you have visibility.
Rebus helps warehouse leaders move from fire drills to foresight. You’ll spot issues before they escalate. You’ll shift resources before the backlog grows. You’ll prevent missed shipments instead of making up for them after the fact.
That’s not just better warehouse visibility, that’s better business.
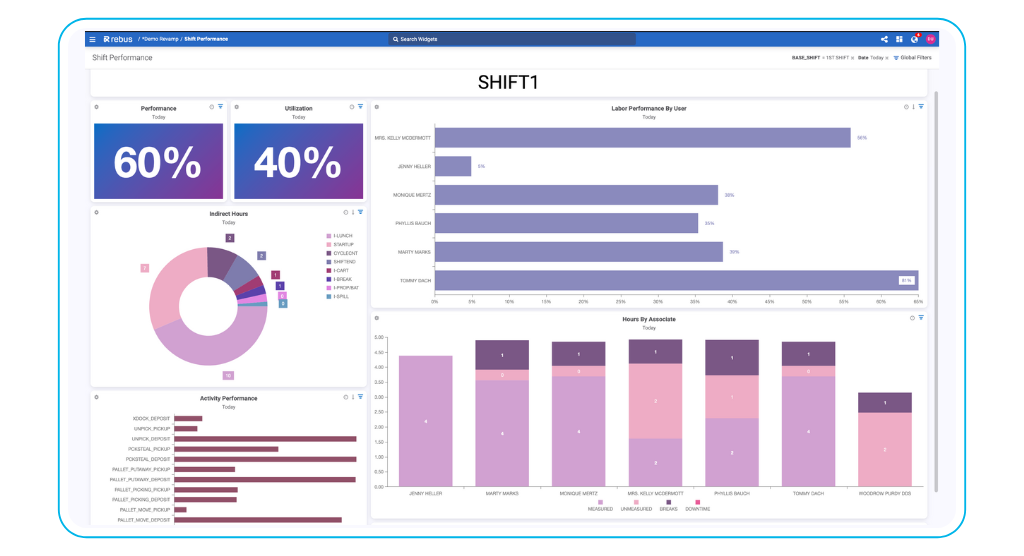
Smarter Warehouse Visibility Starts Here
If your team is still managing your warehouse with spreadsheets, radio calls, or out-of-date dashboards, you’re working harder than you need to. There’s a better way.
With Rebus I&PA, visibility becomes your superpower. You’ll understand your warehouse like never before (who’s doing what, where help is needed, and how to make every labor hour count). You’ll reroute with precision. You’ll adapt with speed. And your warehouse will run leaner, smoother, and more confidently with every shift.
Because smarter warehouse management doesn’t start with the schedule. It starts with what’s happening right now, and whether you can see it.
Learn more here or schedule a demo.
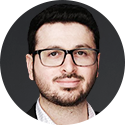
Author Bio
Edip Tac is Director of Sales Engineering at Rebus, where he’s spent six years advancing supply chain technology in hundreds of facilities. He thrives on solving complex challenges, whether working with traditional WMSs or homegrown systems, from optimizing warehouse operations to advanced inventory management. Edip excels in shaping logistics through strategic thinking and cutting-edge solutions.
Never miss a story. Stay updated about Rebus news as it happens.
Read more about closing the visibility gap: https://www.inboundlogistics.com/articles/tips-for-closing-the-visibility-gap/