Insights and Takeaways from NOW 2024
Leigh Chesley hosts a roundtable discussion with members of the Longbow and Rebus teams as they review some of the key insights from NOW 2024, held in Montréal in August....
On August 29, 2024
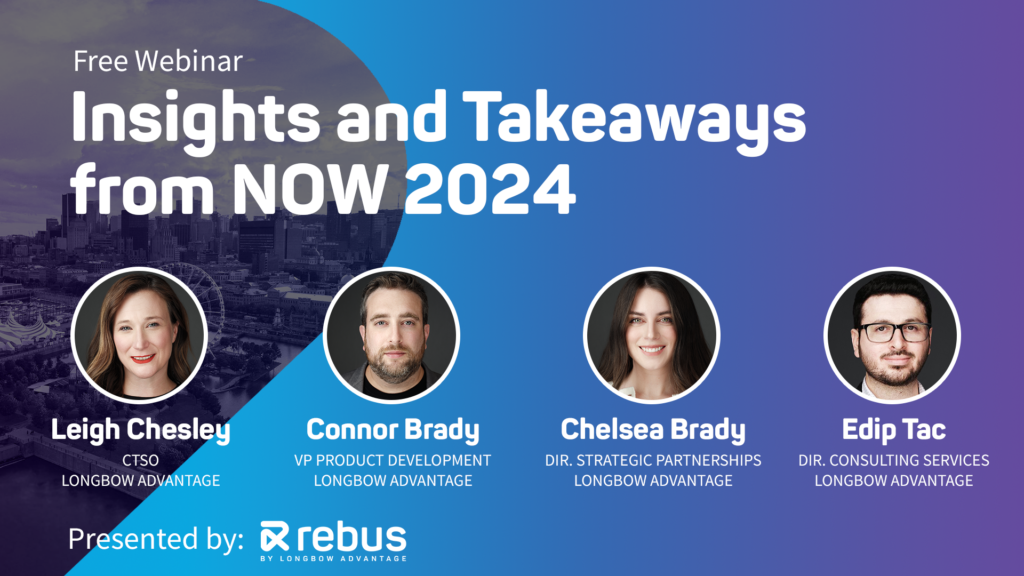
Leigh Chesley hosts a roundtable discussion with members of the Longbow and Rebus teams as they review some of the key insights from NOW 2024, held in Montréal in August.
With the theme of Navigating the Future: AI Solutions for Supply Chain Challenges, many of the speakers and sessions explored the impact AI has had on the supply chain so far, as well as what the future holds. Get the exclusive highlights from those sessions!
As a bonus for Rebus users, you’ll also get a sneak peak at the roadmap for future Rebus innovations and learn how to use your real-time data to inform your decisions in ever more powerful ways.
Watch the replay for free below!
Hosted by
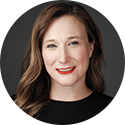
Leigh Chesley
Chief Strategy & Transformation Officer
Longbow Advantage
Speakers
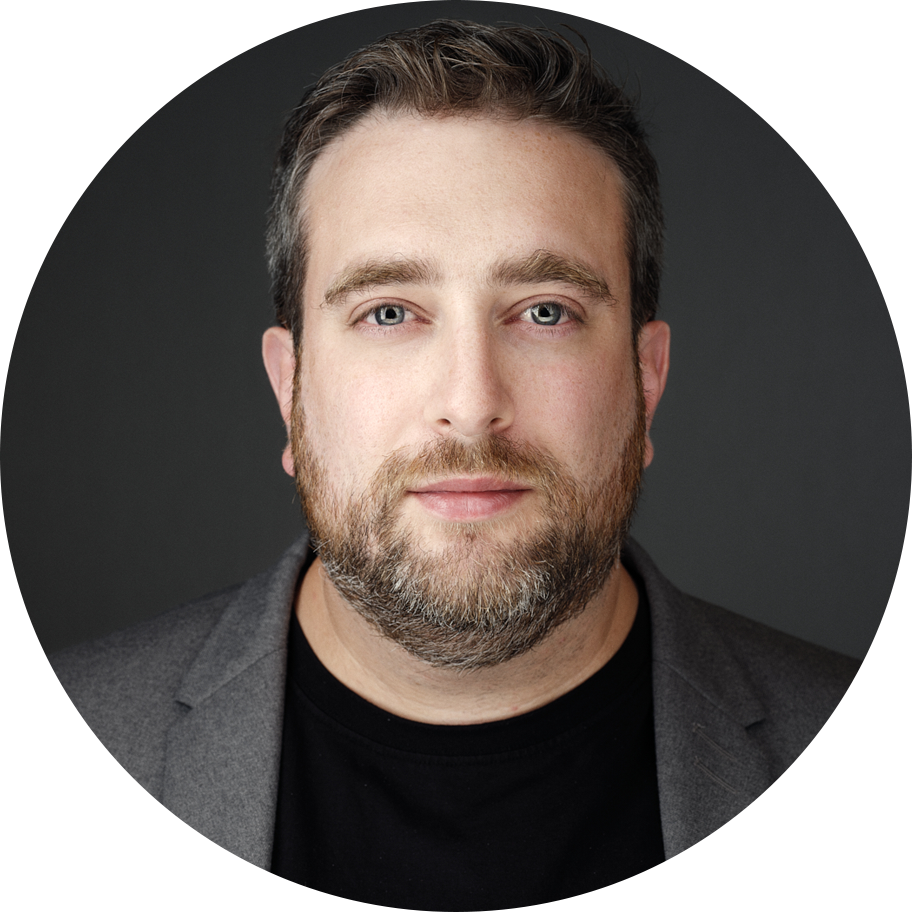
Connor Brady
VP of Product Development
Longbow Advantage
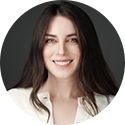
Chelsea Brady
Dir. of Strategic Partnerships
Longbow Advantage
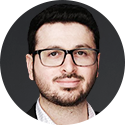
Edip Tac
Dir. of Consulting Services
Longbow Advantage
Webinar replay
Transcript
Hey everyone, and thanks for joining us today. My name is Leigh Chesley. I’m the Chief Strategy and Transformation Officer here at longbow, and I will be your moderator today. We’re going to spend the next 30 minutes sharing high-level takeaways from NOW 2024 our annual customer conference that just took place last month in Montreal. So although we wish you could have been there for the networking, the poutine, Casino Night, all of the fun stuff that that we had this year, we’re really excited to have you here today.
So I’m joined today by Connor Brady, our Vice President of Product Development, Chelsea Brady, our Director of Strategic Partnerships and Edip Tac, our Director of Consulting Services. So this incredible team of Rebus experts will cover a wide range of topics, including insights into our product roadmap, labor management success tips, warehouse maps use cases, and we’ll wrap up with some tips and tricks for better data visualization, which I know everyone is very excited for.
Before we dive in, I’d like to remind you that you can submit questions at any time through our chat, and we’ll do our best to address them at the end of the presentation. And of course, your Rebus Customer Success Manager is always available for feedback and questions after the session. So let’s get started. We’re diving right into a product announcement, and in this first section, Connor is going to take us through the powerful innovations coming soon for Rebus. Connor, over to you.
Thanks, Leigh. Good afternoon, everybody. Thank you all for being here. So I’m going to try to condense what was a 30 minute presentation at NOW into something around six-ish minutes. So let’s get right into it.
Okay, so I presented this at now, and I present it every year that I’ve done the product session at NOW, and I wanted to sort of keep that tradition going, just wanted to highlight some of the numbers that we have underlying Rebus.
You know, we have over 41 terabytes of customer data, 15 billion records from 400 different data sources, we’re collecting data from over 500 warehouses, Rebus LMS tracks labor for over 30,000 warehouse employees, we ingest about 400 gigabytes of data per week, and we get about just over a million data requests from our UI and APIs every single day. So we continue to see really amazing growth, both from a visibility and labor data perspective. And so with that being said, you know, we wanted to discuss with you today how we are leveraging that data and how it relates to our vision for AI and emerging technology.
I wanted to share that vision with you all today. You know, of course, at Rebus, we’re always striving to be at the forefront of emerging technologies and always be innovating. But that being said, you know, we really want to build products with intention and purpose. We want to leverage AI where it provides value to our customers and their operations, and not just build AI for the sake of building AI. And as we know, one of the most important things for any AI or machine learning system is having the right data. And based on the previous slide that I just showed, I think we do what—we know we have the right data, we know we have enough of the right data, and to be able to leverage these types of technologies.
We need to be leveraging our our deep industry expertise. You know, at Longbow, we have, you know, over 60 warehouse management, warehousing experts, excuse me with with, you know, combined hundreds of years of experience, we really need to be leveraging their expertise as we build our products.
The last two are really super kind of the most important to me, personally, one is that we need to be providing flexibility to meet our customers’ unique needs. There are no two warehouse operations that are the same. They are all different in one way or another. And all of our customers bring really unique use cases and really unique stories to Rebus. And we need to be able to be providing them with products and functionality that are flexible enough to meet those needs.
And then lastly is remember the human. I think, for me, this one is extremely important. You know, we really need to continue to strive to improve, to provide products and functionality that are easy to set up and easy to use, and always remembering that there’s an actual person, you know in front of a screen who’s using Rebus, and we want to provide them with with products that are that they are enjoying using and want to to to work with every day. So with that being said, we are very excited to announce Rebus AI Trend Forecasting.
So this marks. A major step forward for the evolution of the Rebus platform. Trend Forecasting is the first product that we’ve developed that leverages the benefits of AI and ML to bring greater—to bring even greater insight into the data that you’re already bringing into the Rebus platform. Those hundreds of gigabytes per week that I was talking about. So what is Rebus AI trend forecasting, and what are its capabilities?
So AI Trend Forecasting, like I said, is our first major AI initiative as a product. AI trend forecasting allows you to take the data that you already have within Rebus and generate AI-based predictive forecasts into the future. It’s not a labor forecasting specific tool or demand forecasting specific tool. It’s both, and it can actually do more. You can really create predictive forecasts for any time series widget that you have in Rebus. It’s all done with your existing widgets, and it’s super easy to use, you can compare your forecasts with the actual data that’s happening in real-time, and then tweak your forecasts to find the best match as you go forward into the future. And as with any AI tool, as your widgets gather more data day after day, all that data that we’re ingesting into Rebus, our AI models can capture more accurate results.
And then lastly, it’s integrated directly within Rebus is Widget Builder, so you can query and chart your forecast data and create dashboards just as you would with your warehouse data. So just wanted to go cover some of the ways that we feel that Rebus Trend Forecasting can help warehouse operations. So first is, you know, around inaccurate forecasting, we know that forecasting is hard using simplistic, you know, a lot of our customers use, sometimes simplistic Excel formulas based on static data. And you know, in this day and age, that really just doesn’t cut it. It leads to higher costs and increased risks.
With AI Trend Forecasting, we’ve you know, it can really help you get better, more accurate forecasts based on your actual data and up-to-date data that is constantly being updated in near real-time. The second is inefficiencies of manual processes, which means you can’t really react as quickly as you need to in an ever changing, disruptive world. Like you said, Trend Forecasting is super easy to use. Can be set up in minutes, and really allows you to get forecasts of your data in a very, very quick turnaround, so you can be able to react more quickly.
And then lastly is, you know, issues with fragmented systems, having disparate tools. You know, maybe using one tool for one side, another tool for another, Excel or some, some other forecasting tool creates a lack of cohesion between your operations. And you know, one of the main value propositions of Rebus is that, you know, with Rebus, you’ve already got all of your warehouse, your warehouse, is sending data into Rebus and being able to visualize and access that data from a single pane of glass. So you can generate forecasts for all—for any region, for any facility, for shifts, for different activities and on and on and on. It’s all in one place. You no longer have to go to different tools to get different forecasts.
And then I also wanted to cover here just a few trend forecasting use cases. Obviously, you know, there’s labor supply and demand. Being able to predict labor hours and adjust for shifts in demand and changes in the workforce. Inventory demand, inbound shipments, outbound shipments, you know, being able to predict cycle counting needs, being able to predict warehouse capacity utilization, you know, to be able to project warehouse capacity into the future, and so on and so on.
Like I mentioned earlier, you can really predict any time series data. So any data that is bound by a date and is a number, we can predict that into the future. And before I wrap up, I just wanted to share a few screenshots. So we did a live demo of Trend Forecasting at NOW, so I was really able to convey the simplicity of use of this tool. But I wanted to share some—we don’t have time for that today, so I want to share some screenshots. We have a new page in Rebus where you can easily create and manage your forecasts. Really all you got to do is select the widget that you want to build a prediction for, select which field you want to build that prediction for, and then which date range you want to predict into the future. It’s really as simple as that.
Once the forecast is generated, you can build widgets with the forecasted data, and you can even overlay that forecasted data on top of the original widget that you used to build the forecast from so you can track its progress and accuracy as you move forward in time. You can see the example that you have right there in blue is the actual widget that we were forecasting. And that red on top is the forecasted data that was generated by our AI model. So that’s Trend Forecasting. We’re super excited to be launching this product. We think you’re going to love it. And really, this is just the beginning. We’re going to continue to add more features, more functionality as we go forward. And so with that, I’ll hand it back to Leigh.
Awesome. Thanks, Connor, for that fantastic overview of Rebus AI Trend Forecasting. I know one thing that really stands out, and I know you’ve heard this from customers, is how exciting it is to be able to use their existing data and make accurate predictions for labor demand, really anything that Rebus has visibility into. And I also know the ability to tweak those forecasts and see the real-time results is something people are super interested in getting their hands on. So really looking forward to the impact that this is going to have for our customers.
So speaking of forecasts and real-time results, we’re going to turn our focus to labor management. Chelsea joins us now to share how labor strategies can make a real difference in both day to day operations and in long-term success. So Chelsea, over to you.
Thank you, Leigh. So I had the absolute pleasure and honor of presenting this session with with Andy Hunter from Connors Group. They are one of our our top partners, we work very well together. Between the Rebus tool and their their incredible services around labor programming and labor standards, we complement each other fantastically. Unfortunately, Andy is not here with me on stage today, although he assured me he would be a participant. So if you do have questions, I’m sure he’d love to to sort of help, help us out in the answers as well.
So as we move forward, we’re going to talk about the the takeaways. So like Connor said, he had a 30 minute presentation that he’s now condensed into five minutes. Ours was an hour. There was a lot of information. Information that there’s no way we can get to all today. However, we will continue to build upon what we discussed and publish with everybody out out in our customer base, so they continue to learn as we as we do as well.
If there was one takeaway I would like everyone to come out of today, and I hope everybody came out of from NOW, it would be really around how labor management is not just a tool or a system. It is really—that is a part of it, that is an integral part of it, for sure—but the overall labor management is a program. It is something that is both in combination with your team, as well as with the systems and the tools that you use to support it. So labor management program really is built up of quite a few things, including a huge part, which would be change management. There would be how you’re setting up your standards, and this is where a lot of the content came from.
So if you would think of the program as an umbrella, and the pieces that we spoke of all sort of wrapped in under that umbrella. Connor’s Group really are extreme experts at labor standards, and I could never do it justice to reiterate what all the information Andy provided, however, it is something that I want to make sure we bring up today, that when you speak of standards, it is super important, especially when you have a large network, you’ll get a lot of your ROI based on having UPH and understanding the hours in your building, your your downtime, your non-productive time. But if you’re really searching those extra few percentage points on ROI, standards is where you want, where you want to be looking at next. And Connors Group have developed a really great way to do that, in a way that is cost-effective, that is time-effective, and takes a lot of similarities between your network and rolls them out across the board. So similarly to the way we scale Rebus, they will scale their their labor standards as well.
We also talked just about how the program and the tool itself are not just something that you implement, but rather something that you maintain, and that as anything else in your in your operation, it deserves the time and the appreciation of a good program that needs to be sustained. So maintenance and sustainability was another huge part of our discussion that we wanted to share with everybody. It’s not a set it and forget it type of solution.
So as we move forward, a few things I wanted to just share with everybody, some of the key takeaways in terms of the content was really around, like I said, change management. So Rebus is part of the solution, but change management is something that should be at the forefront when you’re deciding to implement a labor program, and it should. Continue to be a forefront—in the forefront—as you sustain your program. Everybody wants change. I thought this was such a great representation of change management for companies. So everybody wants change, but really, at the end of the day, nobody wants to change. And that is something that through, through your culture, company culture, and through communication, you should be able to foster as a whole, as a group.
And then just shifting gears, one thing I wanted to highlight was really important around sustainability, and specifically, because we’re looking and speaking to ROI, is making sure that you are defining your success criteria: what are the KPIs that you will be tracking, and making sure that they are set up and that they are there from day one so you can continuously look at them as engaging your your entire network and your entire team of, whether it’s senior leadership, right down to the employees that you’re working with every day, making sure that everyone sees what the KPIs and the benchmarking is and that we’re trending in the right direction. It not only helps to get the continuous funding and support for the program, but also helps with the motivation factor of just seeing the progress happen on a day-to-day basis.
And then finally, just, you know, a last transition, something I wanted to make sure we we did touch on that. Like I said, a big topic was sustainment and maintenance of of your labor tool. Often people think, you know you’ve—or not that they think—but you’ve put so much effort into setting up and to configuring your labor tool, and then it sort of falls out of priority.
There’s a lot of key metrics, and really you want to be able to use your analytics, not only for the benchmarking, not only for coaching and performance opportunity, but to be able to take those, take the data that you have, and make sure that you’re continuously updating and tweaking your your standards, your your indirect time, your non-productive time, so that it reflects where you are currently.
I think, just to to wrap up nicely, if, once again, I’ll repeat it, just because it is so important, we will continuously be talking about how the labor program is is not just about the tool, but it is really a combination of the people and the tool and the communication that goes with it. So I hope that was a good five minute recap.
Awesome. Yeah, thanks, Chelsea. I think the team here knows that I could talk about change management for hours as well. So really appreciate you sharing that with us. Um, now we’re going to dive into another area of operational improvement next, which is Warehouse Maps. So next up on the stage, I’m going to have Edip joining us to walk through how Rebus can help identify bottlenecks and optimize warehouse capacity. So Edip, the floor is yours.
Thanks. Leigh. So one of the sessions that I led during NOW 24 was actually the spotlight, kind of, for our warehouse maps visualizations. I actually introduced How to Set Warehouse Maps Up at NOW 23 and this year, we kind of wanted to present a few use cases that we’ve been working with our partners at Mars Petcare. And essentially, we wanted to inspire folks that were there with us at the conference, and hopefully also those of you who are on this webinar on how you can leverage Warehouse Maps in your operations.
Now, why do we need Warehouse Maps? Well, we’re all used to seeing bar charts, trend lines, and grids to kind of dive into the data, but as the saying goes, picture is worth 1,000 words. So the human mind, as we know, is able to recognize patterns and drive conclusions and actions from kind of looking at these top down bird’s-eye views, especially of your operations. So in that regard, with Warehouse Maps, we’re able to get that top down view into your operations and easily make decisions to ensure you have successful operations and can focus on winning the day.
So with our approach to this new visualization layer, we’re able to overcome some of the challenges trying to locate inventory, look into hotspots of heavy, kind of, you know, foot traffic, so we can kind of work through operational inefficiencies and speed up the overall order fulfillment process by eliminating such bottlenecks. But perhaps one of the main challenges I’ve seen our clients and partners leverage Warehouse Maps for though, is the kind of inefficient user space. You know, since we can, at a very quick glance, identify locations with very little or no inventory that will be ideal candidates for consolidations, that allows us to free up wasted space. And as we know, space is a precious commodity within a warehouse, and the metric you’re actually seeing on the left of the slide here is actually what drives just that: green locations have fewer pieces of inventory versus the red locations that are at full capacity.
So how did our clients already start using Warehouse Maps when we just announced it the time before? Well. The team at Rebus actually has built the Warehouse Maps module by leveraging leveraging an app-based editor approach. So essentially, you can either upload a CSV for XYZ and have the platform build out a map for you immediately, like the view we just saw earlier, or you can take that Lego like approach, where it can build a location by specifying how long, high, deep a location is, then build a rack and build over from there, and just drop the pieces together and build out the map like you would a Lego set. So essentially, combine smaller pieces, build it up to a rack and then put those down on your editor to go ahead and build out your warehouse.
And then we’ve also added automated labeling approaches within the tool, so that if you’re building it out yourself, you can label the map out as you’re building it very, very easily. And as Connor also hinted, even for this layer here, we’re actually building upon our Widget Builder. So the clients and partners and those over here are already intimately familiar with Widget Builder, so we can leverage existing metrics or very easily build new ones to kind of integrate with the map. And as everyone is familiar with Widget Builder, it makes the process very easy, and the system allows you to select colors such as red and green, like we saw again in the previous example. It’ll automatically fill color intensity between your choices to highlight High, Medium, Low kind of approaches to the data without you having to sit there and kind of specify each color range one by one by one. And we’ve also incorporated drill downs into the Warehouse Maps, which means you not only get that top down view, and you can get some insight using tooltips, which you’re already familiar with, some of your existing widgets, and I’ll show you an example in a few slides down. But you can also drill down and gain insight into the data at a granular level, if you wanted to as well.
So I want to talk about a few high level use cases we’ve seen our clients leverage, and also few that we’ve internally kind of tried ourselves as well. So as mentioned, the capacity and location utilization are kind of the first ones that come to mind, since you get a top down view of all locations in one easy to digest view. But since we can achieve heat maps of the color sets that we’ve set, we can also highlight most visited locations. We can make decisions on potentially spreading out inventory to avoid congestions. Or we can also determine what are all the locations that have and have not been counted in your current cycle count period, to also identify those locations or areas that might not have as accurate of inventory levels, since we haven’t confirmed the inventory in, potentially a substantial period of time.
And last but not least, while we do call them Warehouse Maps, they are not just bound to the four walls of your facility, but rather a way to facilitate your warehouse operations, and the yard is a key component of that. So here we have a facility of one of our partner sites that leverages Rebus for yard management. This is actually the Google image of the facility that we’ve cleaned up to remove, kind of the trucks outdoors and overlaid our map components on top of the image. So each rectangle that you see here represents a trailer position. Clicking into each trailer shows details about the location by the tooltip I mentioned earlier, which then kind of gives you that insight into what’s the trailer in the location. What is the shipment ID associated with it, how many pallets, if any, are in that trailer, and the top down view also gives you that quick insight into what your yard status is. This also kind of allows you to bring new hires up to speed a lot faster, since you can point at a particular location on the map and have them quickly take a look at the location and move a trailer in or out of it with ease, since we’re eliminating that learning curve of learning the yard layout and the naming conventions.
Another use case we also shared at NOW 24 was aisle congestions. So since we have labor visibility, data of the facility, we are able to in near real-time, indicate how many picks are coming out of each aisle at what time of day, and highlight hot spots where heavy traffic can occur. So this allows us to, for example, in this view, quickly identify which of the aisles will be the busiest for today’s operations. So as with the color gradient here, we can very easily see that aisle 36 is the busiest with 42 picks, followed by aisle 54 which is the second busiest with 30 picks. But we can go even deeper within the same view by essentially toggling the layer that represents how many picks are happening at an aisle at each hour of the day. Now we can see that aisle 36 has 29 of those 36 picks actually coming out of it at 12pm local facility time, and the supervisors can now go ahead and take initiative and maybe move some of those picks up the schedule so they can open the open inventory up to end caps or open storage locations or staging locations, sorry, and kind of eliminate that congestion that could happen when the loads that these inventory tied to are due. So with that, I’m hoping that gives everyone here a little bit of an insight as to how we can leverage Warehouse Maps to guide you in running your operations as efficiently as possible. If you have any questions, feel free to shoot a note in the chat or reach out to your customer success representative and Leigh, I’ll kick it back to you.
Awesome. Thanks, Edip, I know so many customers are seeing significant improvements, you know, tracking, location utilization, having better visualization in their warehouse. I believe we even have another webinar coming up October 10, where we’re going to get into that in even more detail. So speaking of easy to read visuals, next, we’ll take a look at some quick wins and tips for clean dashboards and better data visualization. So Chelsea, back to you.
Great, thank you. So I’m very cognizant of time here, and I think what I’d like to do is just, let’s keep moving forward. And I’d like to talk through using visuals, and in this case, since it is based on data visualization, just to kick it off, the thing I would highly recommend is, when you are building a dashboard, think of who is the end user. So before we get into the actual visual key elements that I like to look at, I would just suggest that you think about the end user. And sometimes it’s hard to remove, remove yourself from the position that you’re in where you’re so, for lack of a better term, “in the weeds” and so easy to follow in your mind. It’s not always the case for for somebody else, I would sometimes I even ask my my my friends, just take a look at this. Could you read this quickly? So just little suggestions to make sure you’re not tailoring something that is is too specific for your own needs, and rather for the broader audience.
As we move to the next visual, the other thing I would just like to say is we do focus so much when we’re working with our customers on the data accuracy, which is such a huge, huge importance to our customers, and as it should be. But when you have that data, that accurate data, the best thing I can say, or the next best thing, is really working on your visuals. So instead of it being a sort of after the fact type of, okay, now the data is perfect, let’s just throw out some metrics for people to start using. Think about the visuals, because what tends to happen is that they are too confusing, too cluttered. There’s there’s too much, there’s too much going on to really understand where you should be looking at. So try to, instead of having visualizations be an afterthought, make it maybe an initial thought as you work through the data accuracy. So they really should be equally as important so that the end product is is usable, both from an accuracy standpoint and just from a readability standpoint.
So continuing on with with what we’re looking at, I wanted to just show out, show up a couple of examples. So I highly recommend using color coding whenever you can using different types of charts, some bar charts, not all bar charts, not all grids, every every chart should be loved equally and make its way onto your dashboards. This is an example that we built internally for for for our demo environment. And I looked at it and I thought, okay, it’s a really great start. But how can we make this better? How can the end user open this up and get a really clear picture without having to necessarily even read everything that is on the dashboard to get a yes or yes things are good? No, I need to start diving in.
So with that, we’ve we tweaked it, and there we use color coding, as you can see, to really draw your eye to the sections of the screen that you want to stick, that you want to be combined together, where you want the eye to be directed, and just those small, incremental differences make a huge impact to the end user and their ability to pick up new dashboards, pick up new KPIs, and run with them right away.
So as we continue, I’d also just like to say, with an example, there’s so much data, like Connor mentioned in his original slide, we have massive amounts of data, and we’re in a big data era, era. Everybody wants their data. The caution, I would say, is data is super important, but make sure it’s the right data. You don’t need every single piece of data. If you could see the this on the screen, the top metric is giving you every single user, I believe, and then the bottom one is, well, don’t give me every single user or every single location that’s having an issue. Give me the top five or the top 10 so that I can take action on those. So while data is important and we need a lot of data to make decisions, we don’t need all the data. We need the right data.
So these are best practices. I’m just throwing them out there. These are things that I use on a daily basis as I am either building out my own dashboards, as I’m helping our team build dashboards for our customers. Just think about simplicity. Think about the story that you’re trying to tell, and then make sure you’re using colors, make sure you’re using your fonts properly, that things are sticking out where they should be sticking out, and that your are your eye is being drawn to. The right place.
So with that, we did have our second reveal of the conference. Our next up and comer is the Design Chart. So again, just cognizant of time, I’m going to rush through it, but hopefully in an impactful way. Everything that I showed and everything from a widget, a properties aspect, or the way the widget looks, is the the functionality is not is not changing. We’re not adding additional ways to view your your widgets, but what we are doing is making it easier to update them, and making sure that the initial when you land on a widget, it looks good, and you’re not spending as much time focusing on how to tweak the colors, how to tweak your fonts, how to tweak the alignment. It’s really a much user friendly, much more user friendly way to build your metrics to hopefully get it out faster and nicer looking with more impact.
I did have another example I just wanted to show so that you can see we’ve revamped our color themes and everything. As Connor mentioned, we’re keeping the end user and the human in top of mind as we redesign these things. So hopefully this helped to give some just quick tips and to see what’s possible and know that we’re giving back our customers the ability to do that in a really quick and seamless way.
Awesome. Thanks, Chelsea. I’m always blown away by what just a few of those small tweaks can do to help make important decisions much easier for operators as they’re looking at the data they’re consuming on the floor. So before we wrap up today’s session, you know we can open the floor for some questions. You can continue to submit as many as you have for your speakers. We’ll, we’ll stay on and address what we can I know we’re a couple minutes over, and then if there’s anything that we didn’t get to or anything you want to follow up with, you’re welcome to, obviously, always reach out to your Customer Success Manager, or you could reach out to myself or anyone else on the panel as well.
All right, so “what advice do you have for organizations just starting to implement labor as part of their broader operational strategy?” Chelsea, I think we’re going to kick that one over to you, if you don’t mind.
Of course. Yeah, absolutely. So I’ve actually been looking at this one since it was asked for a few minutes ago. So really, the thing I would say is understanding those baseline KPIs. What is your what is leadership looking to? What are they looking to gain from having a labor management solution and then building your program around that. If it is reduced, reduce indirect time, for example, make sure that’s a key metric that you’re tracking, making sure it is a main focus in your communication, and then I would say the the best piece of advice I could give is, as you’re building out your communication plan, make sure that your your workforce feels like they’re part of the decision. Make sure they’re part of what you’re implementing to sort of soften the blow of the change. Really, labor management should be something that incentivizes people to do better on a day to day basis, to like where their place of work. It’s really meant to be a positive tool. So make sure that they’re part of the planning, part of the communication, and really ensure as much transparency as possible with them to get the best results as you start the implementation right up until you get to go live.
Awesome. Thanks, Chelsea. Another one we’ve got here is “what are some of the biggest challenges organizations face when optimizing warehouse space? How are you seeing customers use maps to address those challenges?” So let’s see. I know, I think we’re having a few technical difficulties, but I think we’ve got folks here on the panel that might be able to talk through as well, while Edip is getting back on.
So we’ve been able to use maps in a few different ways when we’re looking at capacity in the warehouse, one is often around air handling, so looking at locations that are that have available, available product that’s not in pickable locations. So there could be just sort of systematic issues with your inventory that is not coming to light, that is not something that you’re looking at that can make a big difference when you’re looking at the overall capacity of your warehouse. So making sure that any inventory that is able to be shipped is in the right locations. Looking for consolidation opportunities. So places where you have partial pallets, where the there’s open bins, etc, you can visualize that on a map. Those are just two of the ways I can think of right now that we’ve been able to help with capacity. And the last thing I would say, as a third, is that we’ve even been able to use maps to recommend overflow buildings for customers. So maybe they’re just at a consistency in terms of maximum capacity, where it’s reducing efficiency of their labor and the the travel throughout their warehouse and so without many other options, and given the the consistency of that, that high capacity overflow was was the right way to go.
Awesome, great. All right. Well, we appreciate everyone joining today, and we will talk to everyone again soon. Have a good day.
Thanks everyone.
Thank You.