Controlling Your Inventory: A Case Study
How can you improve your inventory control and quality assurance processes? Rebus Global Inventory Management brings real-time visibility to your inventory through: It is an essential tool for businesses that...
On February 15, 2024
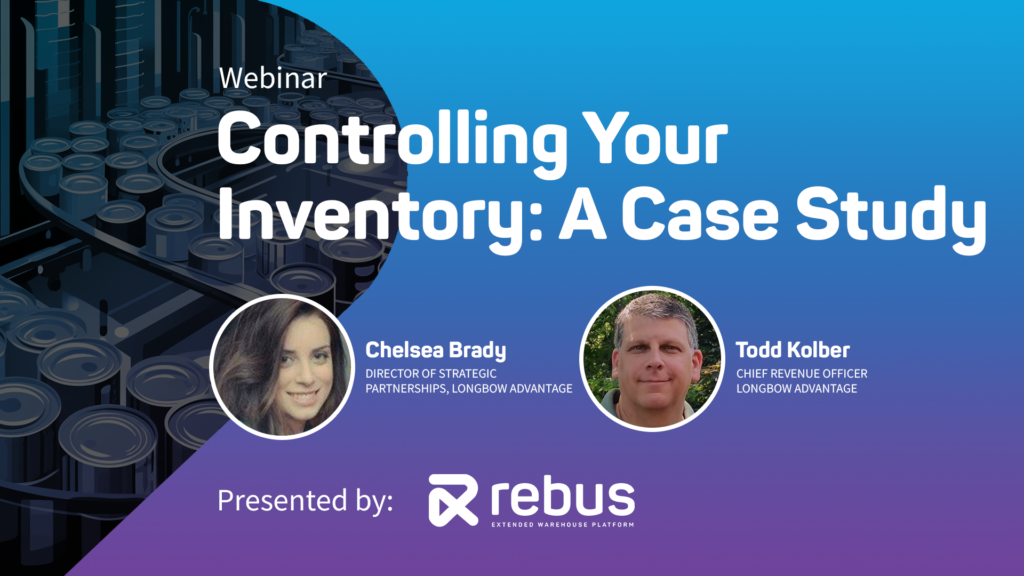
How can you improve your inventory control and quality assurance processes?
Rebus Global Inventory Management brings real-time visibility to your inventory through:
- Inventory Tracking
- Inventory Reconciliation
- Inventory Status Management
- Inventory Traceability.
It is an essential tool for businesses that rely heavily on inventory management, such as manufacturing and distribution, especially Food & Bev. With Global Inventory Management, you can efficiently manage your inventory levels across multiple locations and easily track the movement of products in real-time.
Longbow Advantage’s Todd Kolber (Chief Revenue Officer) and Chelsea Brady (Director of Strategic Partnerships) dive into a case study of one of the largest processed food companies in the U.S. and look at how Rebus’ Global Inventory Management helped them streamline their QA process.
Speakers
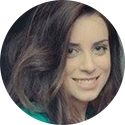
Chelsea Brady
Director of Strategic Partnerships
Longbow Advantage
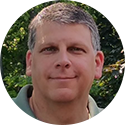
Todd Kolber
Chief Revenue Officer
Longbow Advantage
Webinar Replay
Webinar Transcript
TODD KOLBER
Good morning, or afternoon, depending on which time zone you sit in as you join our webinar. I’d like to thank you for joining us to walk through Controlling Your Inventory: A Case Study. I’m Todd Kolber, I’m the Chief Revenue Officer for Longbow Advantage, and joining me is Chelsea Brady. Chelsea is our Director of Strategic Partnerships, and Chelsea actually led our Rebus implementation team and was the PM that helped deploy the project that this case study is based on, and she’ll be leading you through the actual case study itself.
As we get started, I’m just gonna do a quick overview of what Global Inventory Management and control is as it relates to this case study and our solution. So, there are really four key components to Global Inventory Management control. Those are inventory tracking, inventory reconciliation, inventory status management, inventory traceability. So, what are those things?
So, inventory tracking is just really straightforward. It’s really understanding, from a real time perspective, what your stocking levels, locations, and movement are of any inventory within your entire network.
Inventory reconciliation is comparing your system of record (which for most companies is their warehouse management system) to their ERP, and the data in the ERP is used for financial reporting and compliance for the SEC, FDA, [unintelligable] and so on and so forth, and giving companies the ability to make sure that they are in sync between their ERP and their system of record.
The third component is inventory status management. So, this is managing the actual status on any component in inventory. So as inventory is manufactured, it may be manufactured and released on a QA hold while it’s distributed to a customer, a point of consumption, or into a warehouse. And as that inventory passes through QA hold it may be made available to sell, or it may be held for some other specific reason. Being inventory status management is being able to, from a centralized perspective, view and change and manage and track inventory status.
And then finally, inventory traceability. So, inventory traceability is very similar to inventory tracking. The only difference here is now that you’re opening up the metrics that you use, you may want to look at and query your entire network for inventory based on a point of manufacture, a date and time of manufacture, a specific manufacturing run or set of machines that are processed on, a specific raw material that went into the finished goods. So, it gives you a much more dynamic way of tracking inventory and tracing it based on all components and critical information of the inventory.
So why is Inventory Global Control important? There are a couple reasons. Let me go through them: the first is brand protection.
So obviously companies want to protect their brand, they want to have minimal to no impact on the end consumer. You don’t—nobody wants to have a recall impact something that’s already in somebody’s pantry, or even on the shelf of a grocery store. So, the most important thing is to try to get information around quality issues as early as you can in the product lifecycle, so that you can reduce any potential impact on the end consumer. But you can also reduce the cost of dealing with that issue as you identify it and manage it as early as you can in the product lifecycle.
The second is product quality. So, in a similar way, you’re looking at freshness and managing the freshness and expiry of products. You may have a product that has to flow through incubation, or aging stages before it become available. Managing that process to make sure you’re effectively getting inventory through that process quickly and timely and getting it out into the next stage, with the end goal being that you get the highest degree of freshness at the point of consumption, is critical to your consumer, as well as your brand protection and identity.
And then, and that kind of flows into waste. So, as you’re managing freshness, and you’re managing that process more effectively and staying on top of it, you can reduce waste from spoilage or expiry issues.
There are some other issues that are impacted by Global Inventory Control. One is improved inventory accuracy. So, as you’re managing your inventory, you’re tracking in real-time and you’re reconciling inventory status to your ERP on an ongoing basis. That information now flows into demand and supply planning so businesses can make better decisions on production planning, production runs, inventory investment, so you’re planning and putting inventory in the right markets to meet consumer demand, and you’re not dealing with stockouts at the shelf.
Another one that I think makes common sense, is as you deploy a global strategy around inventory management, you’re now creating standardized reports and KPIs so that all the stakeholders in the process—whether they’re part of your network or your extended partner network—you’re all talking the same language, you’re all dealing with similar KPIs and SOPs, and just that fact (and standardizing communication) leads to more efficient processes and reduces cost.
And then the final one, the obvious one, is food and beverage companies have quite a bit of compliance both at the federal level and industry level. So, a good global inventory management control solution enables you to manage the records and data that go with making sure you’re in compliance with those standards.
So, this drives brand loyalty. And so, making sure that the product is fresh at the shelf, when the consumer wants it, at the point of purchase, is very important to keeping the consumers happy and keeping them loyal to your brand and making sure that they don’t go anywhere else.
And as I mentioned earlier, managing waste, being on the same standards and communication, enables you to become way more efficient, and manage that process in a much more cost-effective way. So, maximizing sales by ensuring brand loyalty and the freshest product is on the shelf. And it’s there when the consumer wants to buy it, and doing it at a lower cost, of course, is going to impact the top and bottom line, making sure your sales remain high and reducing your costs. I think that’s a pretty clear benefit to any program.
So, the question becomes what are the challenges, or what were the challenges, that the company that we’re highlighting here were faced with deploying a solution like this? The first is a large network.
As you can imagine, a large, multinational company has many, many nodes in a network, whether those are manufacturing plants, whether those are mixing centers, forward facing DCS and cross-docks. Oftentimes, there are 3PL partners, which is the case here, maybe other value-added service partners that are in your network that you’re trying to coordinate activities with. There’s a tremendous amount of data in these systems at the line and detail level. And these systems are all disparate. Even within this company’s—and many of our customer’s own company systems—they’re operating across their own facilities, multiple warehouse management systems that they’re trying to coordinate and harmonize information and data.
It’s a challenge in their own systems, let alone when you add in their 3PL partners and transportation partners, and other partners that may participate in their supply chain. There’s a lot of data that needs to be held and retained. And when there is a required query from the FDA or an issue, or potential quality issue, there’s a lot of data to get through and the timeliness of getting through that data is really, really critical.
And most of the management of this, most of trying to solve this, falls on to I.T. departments that are already resource-constrained and heavily taxed—their time is expensive. So, you’re dealing with a constrained resource and a lot of cost to try to address this with I.T. And part of the problem is that there just aren’t tools that are dedicated to doing this and doing this well.
So, it’s kind of a hodgepodge of taking some tools that are in the market, bringing a whole lot of your I.T. and trying to kind of patchwork and make it work well for you. Then you bring in all the internal communication that has to happen within your own departments, and then bringing in your external partners… the communication to deploy a system like this is really challenging. And as I mentioned, there’s not a lot of great solutions—or there haven’t been—a lot of great solutions on the market to enable this.
Those were the constraints that the customer was dealing with when we met them. And they’re the basis of this case study. Since that time, which is roughly about two years ago, the Food Modernization and Safety Act of 2011 has created some more challenges. So, if you’re not familiar with the Food Modernization and Safety Act, just gonna do a real quick introduction to it. But it’s basically a set of rules and, and guidelines that govern those companies that manage and handle food, to, in their words, “share the responsibility of the impact of recall or quality issues in the global supply chain.”
One of the key things that came out of this Act is the food traceability rules. And that’s kind of what I’m going to focus on a little bit here. Those go into effect and companies have to adhere to those rules in January of 2026. So, we’re going to take all that complexity, just shared on the prior screen, and we’re going to add more data and more tracking requirements to it.
There are there are several categories of food that make up the food traceability list that companies that participate in those categories have to work within. There are some exemptions. And if you’re not familiar with those, I’m not gonna go through them here. I’ve offered some examples here, but if you just Google “food traceability rules,” there’s more than enough information readily available to you to, to delve into this a little bit more.
But the critical components of the food traceability rules are events called, “critical tracking events” that are defined by the FDA, that need to be tracked, and key data elements that have to be captured and recorded for each one of those critical tracking events, that companies who participate in in food manufacturing or food handling are required to manage and track. So, who’s impacted by this? Anybody, any company that handles, manufacturers, packages, grows, or holds food that’s on the traceability list.
So, what is the impact of the FMSA?
Well, as you can imagine, there’s now more data that needs to be held than some companies were planning and managing currently. There’s also a requirement that all of the standard operating procedures and practices that go around the managing and handling of food items needs to be very well documented, and those documents need to be able to be shared with the FDA. So, it’s not just the data itself, it’s actually the processes and standard operating procedures that companies are using to manage their supply chain practices in relationship to it.
And the FDA, will make requests on companies based on their suspicion of a contamination event, or an actual event. And companies will have 24 hours to respond to that request. And in the FDA’s words, “in records and reports that must be in an easy-to-understand manner.”
So clearly, they’re looking for some electronic form of very easy-to-understand and identifiable data, which, again, is going to place a burden on I.T. They’re also requiring that data be maintained for two years. So now greater focus on I.T. still trying to deal with the patchwork of traceability and tracking solutions and status management solutions that didn’t exist. It’s really opened the market for a solution like Rebus and we were fortunate enough to partner with one of our customers to create the solution that Chelsea is now going to share with you.
So, Chelsea, I’m going to turn it over to you.
CHELSEA BRADY
Great, thank you, Todd.
So like Todd mentioned earlier, I was quite intimate with this project. I was managing it from a PM, timeline, etc. perspective, but also, I’m really knowledgeable in what we did. So, if you want to throw some questions in the Q&A tab, please go ahead. We’d be happy to answer them.
Also, if you feel like reaching out afterwards, again, I am probably one of the people who know most of the nooks and crannies of this use case and would be happy to offer any additional detail that I can.
So, I think it’s important to look back at our customer’s journey through this process. I think probably a lot of people are used to struggling with visibility into their inventory. I think that’s really just one issue that that arises as we talk about inventory control. There’s, like Todd mentioned, for this specific case, a pretty vast network, 3PL providers, their own distribution centers, a mix of WMS systems, a mix of even versions of WMS within the network. So, it’s a lot of data to consolidate. It’s a lot of different looking data, different look and feel, which often leads to several different processes almost at a site basis, if not by a provider, or WMS.
You can see just having to do one thing one way for one 3PL provider and maybe having to shift that slightly for the next. So really, what we’re looking at is a lack of visibility we had for a customer that managed their inventory from a corporate level and really only had access to the ERP data. And I think we know that’s really only part of the puzzle, where you have the inventory that is being shipped out, the last place you’ll see it is within the warehouse and the WMS. So that was one of the issues. Also having just a challenging time for the management of it, the speed of changing an inventory status when it came up. And it was just extremely error-prone, and led to human error.
Okay, so this is sort of a blast from the past, for myself, anyways. This is what the network looked like before we had begun our project. I should mention that the customer had tried to solve it independently of Rebus prior to us partnering on the project. It took, I believe, between 12 and 18 months before they decided to shelve the project, because it wasn’t really gaining any traction. They weren’t able to get the use cases solved that they were looking to. It was also at quite a large expense, I might add, so it didn’t make sense to continue the endeavor.
So, they were a customer of Rebus and that’s where they brought us in, mapped out their network for us where we really understood what was going on. So, as you can see here, we’re looking at over 75 facilities altogether in North America—primarily in the US. You had a lot that were owned by the customer. They had within their network—outside of 3PL providers—two WMS systems that really looked after a large variety of their distribution network. Then you also had their 3PL providers and amongst them all had different WMS systems. Not to mention the quality assurance team who looked over these facilities and the inventory in those facilities had managed, at a corporate level, which had inventory statuses that were really few, I think there was less than five. Whereas if you correlate those back to the WMS system, we had upwards of 20 to 25 statuses across the board.
So really, you’re asking people to follow a lot of different processes for different facilities, different sites. Phone call was a big one. Email sites, fax sites, that a certain product was going on hold or, or releasing from hold, and really very little visibility into how long it took those updates to be made, whether or not they were being made correctly at the correct status.
So eventually, you know, it was no longer sustainable. And when they came to us, we looked (and knowing our history with food and beverage and understanding the importance of quality and safety) we really went and said okay, we need to find a modern solution to the issues they were facing.
So how they solved it—and I would really say this is a we, how we solved it in conjunction together—we knew that first and foremost is how we get all the data into one place. We can no longer be living in these silos where you can see data in different systems but not all together. So that was, you know, one of the major pieces of the project that needed to be solved for, and then also updating inventory status.
Going back to what Todd was speaking of, time is of the essence for brand loyalty. For food safety, you don’t want to be spending an hour-plus trying to change your inventory status when really, it doesn’t need to be done in such an archaic way.
So, our goal was really how can we help manage inventory status much quicker?
So, this is sort of what the network looks like today. So not only are we bringing the WMS inventory in, we’re bringing it in a way that is normalized—harmonized—so all the data coming in looks identical. It doesn’t matter if you’re SAP, if you’re a Blue Yonder, or Körber, all the inventory data is coming in and is being read in a similar, like way across the network.
We’re also bringing in the ERP data, mainly because what you don’t want is to have people going into multiple systems to try and get a global view of what’s going on. So now we have both sets of data, all under the same—speaking the same language essentially—in the same place. We’ve added, once it’s in Rebus, now we can help the quality assurance team update their inventory in a much more seamless way than [they] were doing prior to working together. And allowing those changes in inventory status to go back to the WMS without any phone calls, faxes, or emails. Lets remove all that, all that nonsense, for lack of a better word. And then allowing the changes in WMS to go back to ERP, which ultimately, by the end, funneled back into Rebus. So, you can get a good view of, or at least an assurance that, the changes that you are making are being taken into account and are successfully being processed.
Okay, so, look, this is a brief view of the platform that we offer, in terms of quality and status management. The goals were to make it easy-to-use. What you don’t want, again, is having something that is hard to train on. I believe for this customer, we had hour-long sessions with each group of quality assurance, or each sort of sub-team of the quality assurance. And by the end, they were able to use the system to a very comfortable degree.
So, we added several filter criteria so that you can track and really summarize the inventory that you’re looking at in a few clicks. No longer do you have to go site by site. “Okay, I have this lot that needs to go on hold. Now which warehouses is that inventory sitting in?” Let’s remove that piece, let’s say, “Okay, let’s look from a lot perspective.” And within a couple of clicks, you can do a mass inventory hold, that takes seconds, a matter of seconds, really.
So, the goal was to keep it simple, easy-to-use. We do have the inventory at the most granular level, so that you can see every detail that is potentially important to you. And then from there, let’s open up and make it a very quick and easy status change. So I can see, “I’ve selected my inventory ABC, now it is at an available status. I’d like to put it on the damage status.” We’re only looking at the ERP statuses to keep the list short and sweet. So that you are now saying, instead of instead of managing 20-plus inventory statuses, you’re only looking at five, and the system knows to send it back to the WMS in its correct status. You have the ability to add a reason code and then also a notification number for proper tracking.
So really, we were looking for an easy-to-use type system, which I think we succeeded on.
Now to add on to the ease of use, we also provide our recorded history screen. So, you can track everything that was done, how the how the inventory was manipulated, by whom, when was it manipulated, when was it changed, so on and so forth, so that you can do that track and trace really simply, really easily, and ensure that the changes that you’re making are being done as quickly as possible—you know, if not instantly, within a couple of minutes maximum. So, a record of the history was very important to provide as well.
So now I think we solved the biggest human error or error-prone problem that the customer was facing. But that was really just MVP for us. That was the minimum use case or pain point that we wanted to solve for. Now that we have all this information, all this inventory data, what more can we do, is really what it came down to. And going back to the Food Modernization and Safety Act, I think there was a lot of opportunity to add visibility, tracking, reconciliation, that that didn’t exist prior.
So, what we’ve done since giving the management of inventory status is a comparison of what you have in your WMS versus what you have in your ERP system. So, I think anybody who knows, or is familiar with managing multiple systems, integration is not always as foolproof as it sounds. So, you can oftentimes end up with discrepancies between the statuses or your inventory in the WMS versus in your ERP.
So now, instead of prior to Rebus, being blind to the fact that something is out of sync, we’ve provided basically a “set it and forget it” type of metric where it’s constantly reconciling the two systems. And we’ll give you the notification, it will send out an email, a text message saying, “Hey, you fallen out of sync with your ERP system or your WMS system, you probably want to take a look at what’s going on.” And you can go further into that and see which details, which inventory has fallen out of sync.
And from a track-and-trace perspective, there was also recalled product. If you need to be providing your, you know, a record, an audit of what has been recalled, where the inventory has been, we’ve provided a really detailed mapping or view of your inventory. So, with some very specific filter criteria, within a matter of seconds, you can pull up a lot number and say this is all the inventory within and this is how/where the lifecycle of that inventory has been.
So, I will finish just by saying that having worked with the team really closely, I think the training and the ease-of-use aspect was a huge gamechanger for everybody. And up until I had to prepare for this webinar, we really never looked back.
[End of transcript]